The end-of-year sales season marks a crucial moment for global retailers and manufacturers. With 20% to 30% of the annual sales happening during this period, companies are looking to tap into a strong consumer demand to end the year on a high note. ​​Yet, with the port congestion driving vessel reliability to new lows, the festive cheer is at risk of a halt for both businesses and consumers alike.
Take for example, the ports of Los Angeles and Long Beach, in California, USA. These two ports combined move more than a quarter of all the US imports. With the average turnaround time at both ports almost doubling this year to 6.4 days – from 3.6 in 2017 to 2019, according to Bloomberg. The time it takes to get products from Asia to North America has now doubled, from around 40 to 80 days.
This has created a ripple effect on many businesses, and in turn, consumers. Nike, for instance, reported that the production and delivery of its shoes in North America would be impacted up to next spring, as it struggles with shipping issues and a worker shortage at its factories in Vietnam and Indonesia, which make three quarters of its shoes. Meanwhile, prices for artificial Christmas trees and decorations have jumped 25% in America due to high shipping costs.
The severity of the congestion has led some of the biggest retailers in the US – including Walmart, Home Depot, and Costco – to charter their own cargo ships to import goods, just to meet the demand.
Unfortunately, businesses without the financial might and scale of these giants might have to bear the burden of these delays on their bottom line. While they have the option of shipping in greater quantities to enjoy economies of scale, there is always the risk of hoarding inventory that can’t be sold, if demand is insufficient.
Additionally, shipping perishable goods, there is the risk of the goods spoiling due to late deliveries. For instance, one of our customers, the world’s largest brewing company, had a beer shipment from Rotterdam to Taiwan delayed for weeks – a delay long enough to have spoiled the beer inside the containers.
Uncertainties are here for the foreseeable future – perhaps into 2023.
Unfortunately, this holiday crunch isn’t a one-off crisis and is likely to stay. As one of the most interconnected industries in the world, the logistics sector is highly vulnerable to macro- and micro-economic factors, and will thus remain volatile.
For instance, consider Figure 1 below, which illustrates the average historical vessel schedule reliability throughout 2020-2021. The average absolute error chart indicates the discrepancy between the latest updated schedule ETA and the actual has been on the uptrend since the start of 2020. This means that even the latest update provided by the carrier is frequently off by multiple hours, sometimes days. And things are not getting any better.
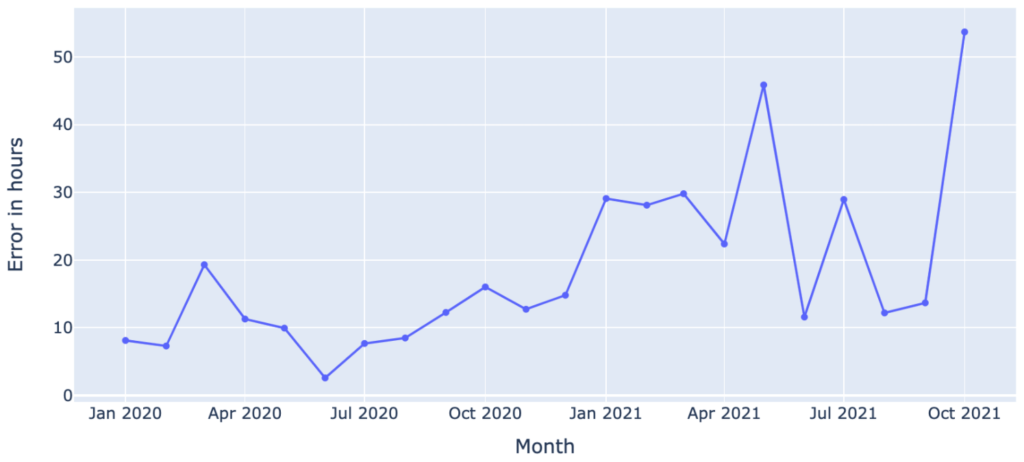
As much as these external factors remain beyond the control of the affected businesses, there is an opportunity to get an edge with more predictive supply chain data. It is imperative for businesses to start investing into savvier technologies to replace current labour-intensive processes.
Why the existing methods will not keep up
Shipping industry operates with vessel schedules and container milestones that are updated at different frequencies, with different levels of granularity and in different form factors. Some are better than others, but none offer a single source of truth that ocean teams can rely on to make operational or planning decisions. For instance, vessel EDIs in port are frequently incomplete or often come in too late (multiple days after the event has happened). Another example is lack of standardisation for some of the key milestones that happen to the container throughout its journey on the ocean and during the port stay.
This leads to an army of ocean operators and logistics teams throughout the globe scrambling through various data sources to cross-verify information prior to making an operational decision. The result is reactive decision making. Days, sometimes weeks late. This translates to additional cost to the shippers which historically, the industry tackled by throwing more human resources at the problem. But as the years of 2020 and 2021 have shown - this does not scale that well.
Portcast’s mission is to help our customers to make sense of this conundrum to enable proactive planning and accelerate the response times when the contingencies happen. Our approach is to leverage cutting–edge AI to process and consolidate multitudes of data sources into simple & actionable insights.
To do that, we use advanced data sets such as geospatial and weather data to understand vessel movement patterns. We also consider wider macro patterns and regional events – i.e. Brexit’s impact on ports around the UK and Eurozone or Suez Canal blockage - to get an indication of the potential congestion building up at ports, or alternative routing options that could be available to the shippers.
Portcast Real-Time Visibility platform is currently being used by both freight forwarders and BCOs alike, predicting vessel arrival with over 90% accuracy up to 5 days ahead of the arrival, whilst the industry average is around 30%. Ocean operators can now use predictive alerts to get more accurate, intuitive and advanced notification of any delays to plan warehouse and trucking movements down the supply chain. In the event of a contingency, better visibility allows shippers to mitigate risks by planning around potential rerouting options, rescheduling pick up arrangements at ports or planning ahead the sales cycles with their customers.Once the journey has been completed, we benchmark carrier based on their reliability, allowing the user to comprehend the historical performance and negotiate better shipping arrangements in the future.
Interested to learn more about how our solutions can be tailored to your business? Fill in this contact form to talk to our visibility experts.