While carriers and ports can manage factors such as infrastructure, equipment, and optimal scheduling managed through appropriate investments and planning, resolution of labor issues generally requires considerable time and concerted negotiations.
Depending on the strength and intransigence of labor unions, the magnitude of port disruptions can conceivably range from slackening of operations to complete shutdowns.
The Situation across the Globe
Globally, labor issues are one of the most common causes of operational disruptions at ports. Regardless of the region or trade lane, labor issues can heavily disrupt upstream and downstream operations at the port, delaying the inland movement of laden containers and evacuation of empty containers, in addition to the cascading impact at origin ports due to the slower turnaround of vessels and equipment.
While the disruptive actions are expectedly limited to the port, the resulting consequences flow across the entire supply chain, impacting carriers, shippers, inland haulage, railroad companies, and end-consumers alike.
The severity and magnitude of the implications of labor-related issues can alter trading patterns and drive the re-alignment of trade lanes.
This was seen during the recent flash strike at the Port of Colombo (a major transshipment hub on the Asia-Europe route), which impaired port productivity levels and has been one of the factors compelling carriers to look at alternatives to Colombo.
In the European mainland, the latest flashpoint is the port of Hamburg, where the dockworkers union has threatened to strike over pay and increased work requirements. Shippers and carriers are justifiably cautious about calling at the port, as is indicated by an analysis of port performance data, which reveals an abnormal increase in the number of vessels waiting to call at the port and a steady drop in vessel departures.
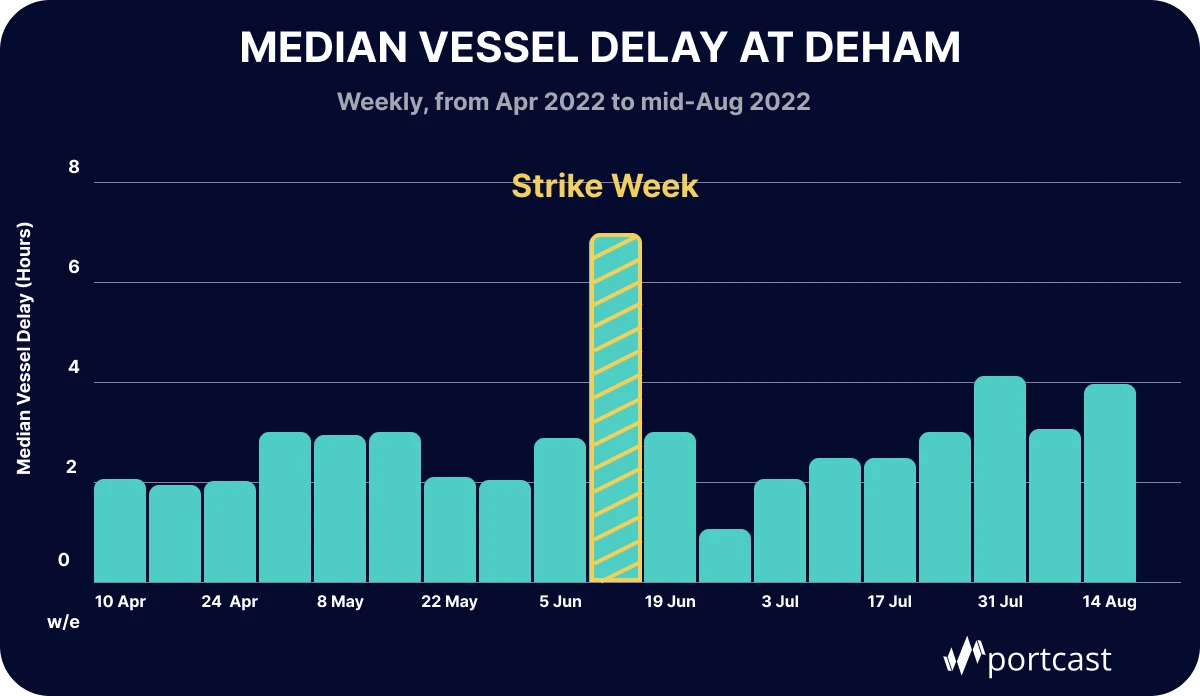
The Situation at US Ports and ongoing ILWU-PMA contract negotiations
In the US, labor is highly unionized, while ownership is vested with private port operators. The biggest ports in the USA are located along its West coast, where the ILWU (International Longshore and Warehouse Union) represents port employees, and terminal operators have formed the PMA (Pacific Maritime Association).
The situation is similar at US East and Gulf Coast ports, where the United States Maritime Alliance (USMX) represents terminal operators and port associations.
Labor contracts are signed for multi-year periods, which means negotiations happen once every few years. With that being said, the present contract is a 3-year extension of the previous contract and expires in June 2022, increasing the tensions between workers and management.
The latest edition of the global Container Port Performance Index developed by the World Bank and S&P Global Market Intelligence rates Los Angeles and Long Beach as the most inefficient ports in the world. This is an indictment of the inefficiency of labor in the US ports sector and hence a key area of improvement for port operators.
Most analysts opine that the PMA will agree to higher wages while the ILWU will reciprocate by permitting automation; however, there is considerable uncertainty regarding the time required to conclude negotiations.
Impact on Port Productivity: Globally and in the US
The impact of labor issues on port productivity is not restricted to the quay-side and cascades down the entire supply chain. While by no means an exhaustive list, here are some of the ways labor can impact port productivity:
- Late or Missed Deliveries
- Container Stockpiles (both empty and laden)
- Imbalance of Exports to Imports (as seen  during COVID)
- Increase in Loading and Unloading delays at Ports
- Increased berth time and ship backlog
- Alteration of Typical (predictable) Shipping Patterns and Capacity
- Higher Transportation Costs
- Deteriorating Customer Service Levels
In the US, the ILWU-PMA negotiations present a grave threat, with the ports of Long Beach, Los Angeles, Oakland, Seattle, and Tacoma at the greatest risk. Considering that these ports are the biggest gateways for US imports, retailers and importers are justifiably anxious about the impact on the shipping industry and overall supply chain.
Steps to Mitigate the Impact of Labor Issues
Some common steps carriers and shippers take to mitigate the impact of labor issues are:
- Import cargo via alternate ports in the vicinity unaffected by labour issues.
- Consider the option of calling at secondary and tertiary ports. Examples include substituting Long Beach with either San Diego or Hueneme.
- Use multi-modal options, such as a combination of sea-rail or sea-road, instead of all-water services. One example is shipping cargo by sea from South Korea to China and then delivering to European destinations using China-Europe rail services.
- Use ports in neighboring countries: a feasible option when there are reliable hinterland connections between the two countries. Recent examples include carriers calling Montreal in Canada and then hauling to American destinations by rail.
- Use predictive visibility platforms which can provide information on vessel delays, bunching, congestion, transit delays granular level, allowing customers to navigate the prevailing uncertainty by optimizing supply chain decisions.
- Being aware of local news, including possible labor disruptions, and preparing contingency plans.
- Building buffers/ storing excess inventory: to avoid shortages arising from extended transit times.